Non-quality in industry: a goldmine to be exploited
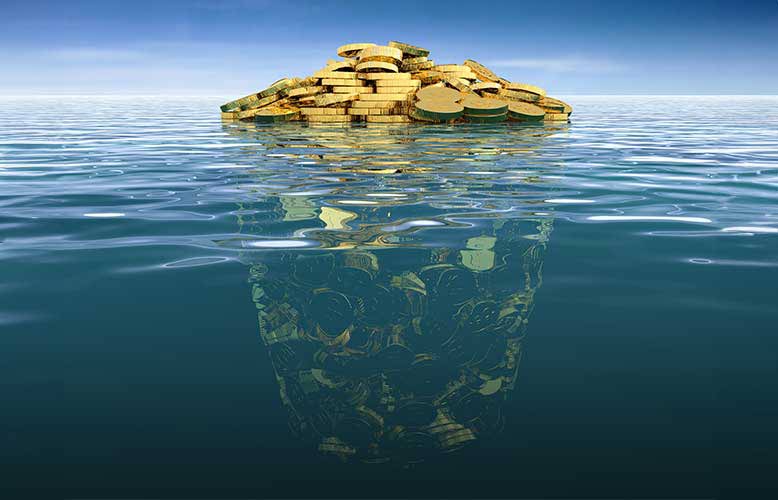
In industry, non-quality is often equated with scrap, with non-conforming production destined for destruction. And therefore the costs of non-quality, to the loss of earnings linked to these rejects. Eventually, there may be a cost to the brand in terms of image. But in reality, this is just the tip of the iceberg. Non-quality has a considerable impact on a company’s structural competitiveness, as it reveals processes that generate waste: material resources, human resources, energy and time. According to a study by the AFNOR group dated December 2023, which can be downloaded free of charge here , 80% of companies estimate their non-quality costs (NCQ) to be between 0 and 5% of sales! And 17% of these companies believe that the share of non-quality costs in their sales will increase, compared with only 8% in 2017. The subject is therefore one for the future, especially if we include behind the notion of quality notions ranging from product non-conformity to societal performance.
Two out of three industrial companies measure non-quality costs
AFNOR’s Occitanie delegation, the Toulouse Haute-Garonne Chamber of Commerce and Industry and the Association France Qualité Performance Occitanie set out to explore this under-exploited CNQ goldmine at a symposium held in Toulouse on December 20, 2023, attended by quality managers from the world of industry. With the message that if you want to fill the mine, you have to put in the resources! Indeed, while 91% of the decision-makers questioned by the AFNOR group in its study said that measuring non-quality costs was necessary or even essential, only 67% actually did so, and 40% systematically defined an action plan if targets were not met. Logically, there is a clear distinction in favor of companies certified to ISO 9001 (the quality standard, which is in the process of being revised) and ISO 14001 (the environmental management standard), which are equipped to track down these costs and the levers for reducing them. But what are the keys to success?
Two industrialists who came to present their approach, Séverine Goldstein for aircraft manufacturer ATR and Damien Lescrinier for Laboratoires Pierre Fabre, were unanimous in their response: the keys are in the hands of the quality function, which must, where necessary, break down barriers and coordinate its approach with both top management and operations. From a managerial point of view, as far as finance departments are concerned, dealing with non-quality must be understood not as an additional cost for the company, but as a profitable investment, thanks to which every error, every loss of time, every anomaly can be converted into profitability-enhancing margins. ” Ideally, the quality function and management control should be involved, and the teams monitoring the process should be multi-disciplinary,” explains Séverine Goldstein.
Involve operational staff in defining measurement and analysis tools
Diametrically, the quality function also needs to get closer to operational staff, who need to see the handling of non-quality not as an instrument of individual control, but as a collective approach to improving their working conditions. “The difficulties faced by operational staff are those of the company as a whole. Workshops also need to be multi-disciplinary, with a global vision”, stresses Damien Lescrinier, for Pierre Fabre. What’s more, operational staff must be fully involved in defining measurement and analysis tools. ” The quality function must not only listen and educate, but also report on successes; team satisfaction and motivation are at stake”, says Damien Lescrinier. “In addition, Séverine Goldstein, for ATR, adds: “Incentives for operational staff to reduce non-quality can also have a financial impact.
For these two speakers, the pitfall of an approach to resolving non-quality would be to exhaust oneself in a desire for an exhaustive inventory and full measurement of all possible and imaginable costs, and thus fall into a discouraging inertia. On the other hand, they feel it’s important to select the most relevant themes, priorities and corrective actions: “For the approach to take hold, you need to initiate change quickly”.