In Franche-Comté, QWL paths lead to ISO 45001
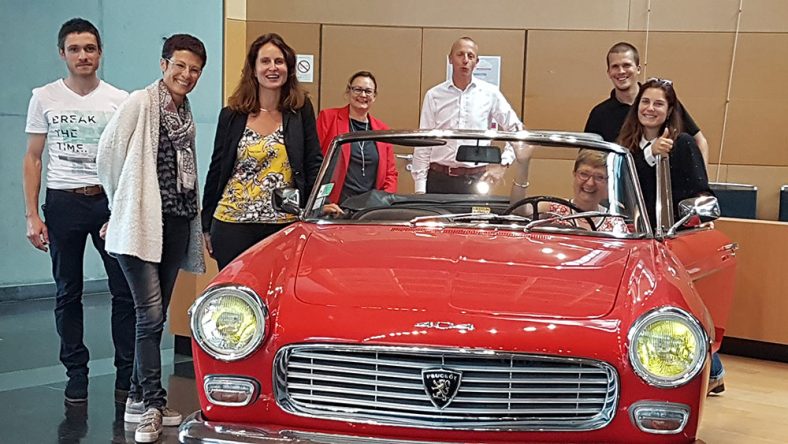
©DR – From left to right: Jérémy Gense (Patek Philip group), Nathalie André and Maud Charpy (Amphénol FCi), Sylvie Forestier and Stéphane Caillat (Patek Philip group), Frédéric Billebault (Stanley Tools), Claire Nicolas (CCI du Doubs).
At the wheel: Paule Nusa (AFNOR group).
A collective AFNOR-CCI operation enabled several companies in the region to share their experiences of quality of life in the workplace.
A club was born, with the idea of leading everyone towards ISO 45001 certification.
When it comes to quality of working life (QWL), there are those who talk about it and those who do it.
Under the influence of Northern European countries and Canada, this subject is now one of the top HR function issues.
And as part of the occupational health and safety (OHS) theme, it touches on ISO 45001, the 2018 voluntary international standard that provides guidelines for deploying an OHS management system.
In France, QWL and ISO 45001 already go hand in hand.
The proof is in Bourgogne-Franche-Comté, where the first AFNOR club of QWL experts has just been created.
The aim is to bring to life the cross-disciplinary expertise of companies in OHS and QWL, and to help them make progress towards meeting the requirements of ISO 45001.
All this, with the support of AFNOR, represented by its regional delegate Paule Nusa, with a training component, in partnership with the CCI.
Going beyond small measures
This traditionally industrial region, home to a large number of automotive and plastics subcontractors, proved to be fertile ground for discussions on this topic.
Whether it’s a question of building employee loyalty or improving management systems, sharing QWL experiences lends real coherence to initiatives already underway.
It allows us to go beyond diagnostics – the traditional questionnaire given to employees – and cosmetic measures – installing a snack vending machine, providing access to a gym.
Club member Pauline Bruneteau-Chapeyron, in charge of human resources at Stanley Black & Decker, a manufacturer of hand tools based in Besançon, started from the following observation: it was difficult to recruit and keep the corporate culture alive at a time when many employees were retiring.
A new lease of life was needed.
”
The training program has enabled us to experiment with actions and tools designed to improve working conditions: tobacco prevention, addiction awareness, open days, family egg hunts, yoga classes…
It’s not every day that we have the opportunity to unite our employees around actions that may seem at first sight remote from the industrial environment, but which concern everyone. “she explains.
The company has thus learned to extend its continuous improvement policy to QWL, as it already does for quality and the environment.
This means that it can now reasonably aim for ISO 45001 certification, along with the ISO 9001 and ISO 14001 certifications it already holds.
Amphenol FCi: a three-pronged action plan
For Maude Charpy, HSSE manager and QWL project leader at Amphénol FCi, a manufacturer of electronic components, quality of life in the workplace is an integral part of the company’s OHS policy, which she monitors on a daily basis with her battery of indicators, including the famous ATMP (occupational accident and disease rate).
Nevertheless, risk prevention and the improvement of working conditions remain key priorities.
” We began by taking stock of expectations, then organized a QVT week, enabling staff to try out physical activities, relaxation exercises and dietary advice.
Finally, we defined our action plan, focusing on three areas: protection against noise, well-being at work, and finally management, with a view to better integrating staff into organizational processes.
Our QWL week was a real success, with 160 participants and a 96% satisfaction rate. “she says.
With the experiences of some enriching those of others, the AFNOR club of QWL experts will play its role as a platform for exchange throughout 2020.
With a common objective for all members: to aim for ISO 45001 certification in 2021, to show that in the field, QVT is not just a hollow acronym.
ISO 45001 audit: fewer non-conformities over time
AFNOR Certification, a specialist in management systems, particularly in occupational health and safety, has compiled its ISO 45001 audit reports, and has come up with an interesting observation: the more recent the certification audits, the fewer major and minor non-conformities are noted. Thus, from April to October 2019 (period 2 in the chart), AFNOR Certification notes just one major non-conformity, compared with 2 from January to March 2019 (period 1) and 8 previously, from September to December 2018, just after the standard was published. The number of minor non-conformities falls from 52 to 31 in March 2019, then rises again. But in terms of the number of reports carried out (17 in period 1; 71 in period 2), the trend is stable: less than one minor non-conformity per report.