
Quality procedures provide additional guarantees to help managers expand into new national and international markets. These are the keys to improving an organization’s operations (whether private, public or semi-public), offering employees better working conditions, and making processes more efficient. They aim to optimize processes, meet customer expectations and continuously improve organizational performance.
Depending on your needs, your field of activity or your level of maturity, the AFNOR group is at your side. ISO 9001, Lean, EFQM, process evaluation, sector-specific quality… An overview of the approaches available to you.
- ISO 9001, the global benchmark for quality management
- What is ISO 9001 and what are its prospects?
- ISO 9001 and other management standards
- The fundamental principles of ISO 9001
- Key requirements of ISO 9001
- ISO 9001 audit and certification: a tool for improvement
- Benefits of ISO 9001 certification
- The ISO 9001 certification process
- ISO 9001 auditor skills and training
- Quality management and global performance
- Integration and complementarity of quality and CSR approaches (or QSE and CSR): or how to use your quality management system to meet the regulatory challenges of sustainable development (CSRD, CS3D, etc.) / Towards a sustainable, responsible approach to quality
- Quality culture: how to encourage and strengthen staff involvement
- EFQM
Quality management: follow the guide to optimize your company’s performance
Our expert Vincent Blache demystifies quality in this two-minute video.
This dossier explores the fundamental principles of quality management, its tools and methods, and its concrete benefits for organizations. Find out why and how to implement an effective, sustainable quality approach.
What is quality management?
Definition and objectives of quality management
Quality management is the set of resources, tools and organizational methods used by an organization to achieve 5 key objectives for its long-term survival:
- sustainably meet the expectations of its customers and users,
- improve business organization, or in other words: optimize operational efficiency,
- reduce non-conformities and associated costs (known as non-quality costs)
- encourage employee commitment
- and constantly adapt to changes in its ecosystem.
This approach is structured around the deployment and monitoring of a quality management system (QMS) specific to the organization. No two QMSs are alike, and it would be counterproductive to try to “copy and paste” the QMS from one organization to another, as each evolves with its own challenges, values, constraints and corporate culture. On the other hand, benchmarking and drawing inspiration from the practices of other companies are highly relevant to the continuous improvement of our own practices. For an overview of quality best practices, we invite you to read the ISO 9001 standard (UAE link: https://www.boutique.afnor.org/en-gb/standards/headlights-standards/standard-nf-en-iso), the international benchmark for quality management.
The importance of quality management in business: why take the plunge?
Quality management is a strategic lever for organizations. Deploying a structured quality approach enables you to strengthen your company’s reputation by guaranteeing reliable products and services, thus attracting, reassuring and retaining your customers (or users). This approach reduces waste and minimizes errors. The result: significantly lower operating costs and higher productivity.
What’s more, quality initiatives help build employee loyalty: employee commitment increases thanks to clearly defined roles and a culture of continuous improvement. This fosters innovation and adaptability to market changes. Finally, effective quality management enables you to better meet regulatory requirements, limiting legal and financial risks. As a result, your company gains in competitiveness and secures its future.
The 7 fundamental principles of quality management
Relevant and comprehensive quality management is based on 7 essential principles that guide organizations towards excellence:
The essential stages of a quality approach
In this video, Vincent Blache, our quality expert, explains the essential steps for any manager wishing to launch a quality initiative and go all the way to certification.
In order to successfully implement a quality-oriented approach, your organization must go through a number of essential stages, the first of which is a genuine commitment on the part of management. Indeed, without a commitment from top management, any quality approach is doomed to failure. Once the project has been launched by management, we identify 5 key stages:
- Analyze your organization to identify its strengths and weaknesses and the external issues that can influence its performance
- Rethink the organization by defining a clear quality policy, aligned with the company’s strategy and broken down into measurable objectives.
- Set up processes in the organization and map its activities, to identify interactions and responsibilities
- Bring the approach to life within the company, to gain experience, train staff and raise awareness, and measure initial results.
- Carry out an internal audit cycle and a review meeting (called a management review) to assess the effectiveness of the approach and decide on any necessary adjustments.
Training and careers in quality management
The quality manager’s role and responsibilities
A facilitator, coach and supervisor (but not controller), the quality manager plays a pivotal role in the implementation and management of the QMS. He coordinates teams and supervises the mapping of activities and the proper deployment of quality tools. His expertise enables him to adapt the system to the company’s specific needs. He/she ensures the involvement of all employees, at all levels of the organization, by promoting internal communication and leading participative workshops. Finally, the quality manager analyzes results and the achievement of quality objectives, then proposes adjustments to optimize the organization’s efficiency. Duties may also include :
- Conducting internal quality audits
- Leading workgroups aimed at continuous improvement and problem-solving
- Quality documentation management
- Preparing for external audits
As the guarantor of the quality management system, the Quality Manager acts as a link between management and operational teams, translating strategic objectives into concrete actions in the field. In some organizations, particularly smaller ones, this role can be outsourced on a time-sharing or full-time basis, enabling the company to draw on one-off expertise to break new ground and support management and operational teams in the discovery and deployment of the approach.
Quality certifications: why not you?
Discover the story of Léa, who called on AFNOR Certification to certify the quality of her products and gain recognition for her good management practices.
Quality certification brings many benefits. It strengthens your credibility, instills confidence in your customers and partners, and enables you to reinforce the optimization of internal processes that you have initiated by launching a quality initiative. Through certification, you demonstrate your organization’s commitment to service quality and operational excellence, thanks to the scrutiny of an independent third party. Regular audits enable you to identify areas for improvement and maintain the momentum over the long term.
Which quality certification is right for you?
- International: ISO 9001
- Excellence and recognition for your transformation projects (EFQM)
- Sector-specific qualities: some players have developed quality certification processes tailored to the requirements of their sector. Examples include IATF 16247 for the automotive sector, EN9100 for aerospace and defense, ISO 13485 for medical devices, and Qualiopi for vocational training.
- Would you like to find out more about our quality certification services? All our services are available on the Afnor Certification website.
- Are you looking for an expert to help you with your certification process, or to carry out your internal audit? We’ll find the right expert for you.
Find out more: quality management tools
There are many tools available for managing a quality management system. Here are some of the most commonly used. Ready to delve into the jargon of quality management? This section is for you!
Process approach and mapping: pillars of quality management
The process approach represents a paradigm shift in quality management. It views the organization as a set of interconnected activities, rather than isolated departments. A process is the set of resources, means and tasks used to carry out an activity (a bit like a recipe: we list all the ingredients, utensils and successive steps required to produce a dish). This method identifies and maps workflows, revealing key interactions and optimization opportunities. By analyzing each step, organizations can :
- Eliminating bottlenecks
- Reduce the time needed for each step
- Improve communication between company departments.
Implementing a process approach implies cross-functional collaboration and increased team accountability. It fosters a culture of continuous improvement, in which every employee actively contributes to the achievement of expected results.
Continuous improvement techniques (PDCA, Kaizen)
The PDCA method and Kaizen, derived from Lean management methods, are pillars of continuous improvement in quality management. PDCA (Plan, Do, Check, Act), also known as the Deming wheel, structures problem-solving in four iterative phases. This approach is a powerful tool for promoting continuous improvement, as it encourages systematic, iterative reflection on processes, enabling adjustments and improvements to be made based on concrete data. It is widely used in various fields, including project management and innovation. The Kaizen philosophy (which means “continuous improvement” in Japanese), on the other hand, advocates progressive but constant improvement. Kaizen is based on the idea that even small improvements, when applied consistently, can have a significant impact on an organization’s overall performance. Its application involves the active participation of all employees, from the operational level to management. The combined use of PDCA and Kaizen creates an interesting synergy, conducive to the continuous evolution of practices and the achievement of higher levels of performance.
Continuous improvement techniques (PDCA, Kaizen)
The PDCA method and Kaizen, derived from Lean management methods, are pillars of continuous improvement in quality management. PDCA (Plan, Do, Check, Act), also known as the Deming wheel, structures problem-solving in four iterative phases. This approach is a powerful tool for promoting continuous improvement, as it encourages systematic, iterative reflection on processes, enabling adjustments and improvements to be made based on concrete data. It is widely used in various fields, including project management and innovation. The Kaizen philosophy (which means “continuous improvement” in Japanese), on the other hand, advocates progressive but constant improvement. Kaizen is based on the idea that even small improvements, when applied consistently, can have a significant impact on an organization’s overall performance. Its application involves the active participation of all employees, from the operational level to management. The combined use of PDCA and Kaizen creates an interesting synergy, conducive to the continuous evolution of practices and the achievement of higher levels of performance.
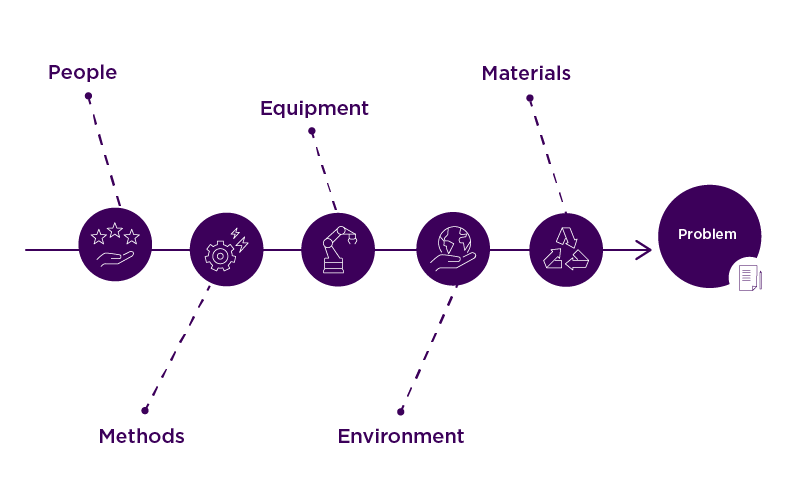
The apple pie example: let’s imagine that a friend has baked you an apple pie and it’s a dud. Potential causes could be related to:
- a labor problem: your friend isn’t very good at baking
- a problem with the method: the recipe was not followed to the letter, or the recipe was wrong
- a material problem: the apples were of poor quality
- an environmental problem: the unsuitable working environment led to measurement errors
- an equipment problem: the oven was faulty and didn’t allow the tart to be baked.
- 5P or 5-Why technique
The aim here is to iteratively ask why, in order to analyze the possible causes of a problem and determine its root causes.
- FMEA
FMEA, or Failure Mode, Effect and Criticality Analysis, is a systematic risk analysis method used to identify and evaluate potential failure modes in a product or process. It is used to analyze the consequences of these failures on overall operation, and to assess their criticality in order to prioritize corrective actions. FMECA is widely used in various sectors, including industry, aeronautics, automotive and healthcare, to improve the reliability and safety of products and processes.
- Would you like to enhance your skills and put these quality tools into practice? Discover our training courses
- Here’s a selection of our dedicated publications:
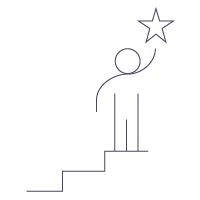
Find out more about the FD X50-819 standard
ISO 9001, the global benchmark for quality management
Discover the international reference tool for setting up, deploying and maintaining a quality management system. ISO 9001 is the global benchmark for quality management. Implemented by over a million companies, it defines the criteria for an effective system aimed at customer satisfaction and continuous improvement. Find out how this standard and its certification can help you optimize your processes, reduce your costs and boost your competitiveness in the marketplace.
What is ISO 9001 and what are its prospects?
Definition and objectives of ISO 9001
ISO 9001 is the reference document describing the steps to be taken to set up, manage and run a quality management system. Its aim is to guarantee the consistent supply of products and services that meet customer expectations and regulatory requirements. This international standard is based on several key principles:
- Customer focus
- Committed leadership
- The process approach
- Evidence-based decision-making
By adopting these principles, companies can enhance their operational performance, stimulate innovation and better manage risk. This standard is certifiable, meaning that any organization implementing it can choose to have an independent third party attest to the successful deployment of the approach, in accordance with the standard’s requirements. This ISO 9001 certification audit also enables you to benefit from the external viewpoint of a professional to help you identify areas for improvement. In this way, certification fosters a culture of excellence, which translates into a better reputation and increased stakeholder confidence.
History and evolution of the standard
First published in 1987, ISO 9001 has undergone several major revisions. The initial version focused on quality control in the manufacturing industry. In 1994, an update extended its scope to other sectors. The year 2000 marked a turning point with the introduction of the process approach and the emphasis on continuous improvement. The 2008 revision brought minor clarifications. Each revision aims to maintain the standard’s relevance to contemporary organizational challenges.
The current version: ISO 9001:2015
The 2015 version of ISO 9001 has introduced significant changes in the approach to quality management. It emphasizes the analysis of the organization’s context and the management of risks and opportunities, reflecting the changing global economic context. This evolution encourages companies to :
- Adopting a strategic vision of quality
- Integrate quality management into business processes
- Strengthening management’s role in the quality system
The harmonized structure facilitates integration with other ISO standards, such as ISO 14001 for the environment, or ISO 45001 for occupational health and safety, forming the QSE triptych. This version also allows greater flexibility in documentation, enabling organizations to tailor their quality system to their specific needs.
A new ISO 9001 expected in 2026: what can we expect?
The latest revision of ISO 9001 was launched in 2023. Publication of the new version of the document is expected in 2026. The fundamentals of the standard should not be called into question: the objective, title and scope of the standard will remain the same, as will the continuous improvement principles of the PDCA approach(plan, do, check, act ). Exchanges between professionals using the standard cover a wide range of topics, including :
- climate change: integrating and taking into account the risks associated with climate change among the organization’s challenges
- quality culture: driving and promoting a quality culture within the organization
- ethics and integrity: responsible, ethical behavior and decision-making with integrity in all parts of the organization
ISO 9001 is evolving to meet the challenges of digitalization and sustainable development. Digital transformation requires quality processes to be revised to include cybersecurity and data management. Companies must now take into account the protection of sensitive information and the optimization of digital flows in their management systems. At the same time, environmental concerns are redefining quality criteria. This has become a key customer requirement. In fact, this is the purpose of amendment A1:2024 published by ISO, which makes climate change a strategic issue by inviting organizations to identify their impacts and risks linked to climate change (to find out more: https: //www.afnor.org/actualites/climat-game-changer-des-normes-de-management/). ISO 9001 encourages the adoption of more responsible practices in the design and production of products and services, through its focus on the efficient use of resources, the reduction of waste and meeting the expectations of stakeholders (consumers and regulators alike).
ISO 9001 and other management standards
Integration with ISO 14001 and ISO 45001: the QSE triptych (quality, safety, environment)
The harmonization of ISO 9001, 14001 and 45001 standards has enabled us to establish a robust integrated management system (IMS). This approach enables you to respond in a coherent and balanced way to the three central issues addressed by these three standards: quality and customer satisfaction for ISO 9001, improving your environmental performance for ISO 14001, and improving health and safety and working conditions for ISO 45001. Switching to an SMI thus aims to unify your process approach and optimize the use of resources by avoiding documentary redundancies. It also facilitates audit management and staff training. As a result, your organization can :
- Streamline operating procedures
- Improving coordination between departments
- Strengthen your ability to meet regulatory requirements
This synergy between standards fosters a culture of continuous improvement throughout the organization, while simplifying the overall steering of the management system. It is also possible to associate other management system standards, depending on your priority issues: ISO 50001(https://www.afnor.org/energie/performance-energetique/systeme-management-energie/) for energy management, ISO 46001 for water management(https://www.afnor.org/environnement/gestion-de-leau/).
Complementarity with industry standards
ISO 9001 serves as a solid foundation for many sector-specific standards. For example, the automotive industry relies onIATF 16949, which adds specific requirements to ISO 9001. This combination enables manufacturers to meet the challenges specific to their sector, throughout their supply chain. In the medical sector,ISO 13485 complements ISO 9001 by integrating regulatory aspects crucial to the safety of medical devices. Aerospace companies useEN9100 to reinforce traceability and risk management controls specific to their industry.
This sector-based approach offers several benefits:
- Better adaptation to specific market challenges
- Greater competitive edge in tenders
- Easier compliance with industry regulatory requirements
Harmonization between ISO 9001 and these specialized standards creates a tailor-made management system, combining universality and specificity.
The fundamental principles of ISO 9001
Customer focus and leadership
Customer orientation and leadership form the basis of a successful quality management system. Clients must place customer satisfaction at the heart of their strategy, by regularly analyzing their needs and expectations. This involves proactive communication and personalized follow-up throughout the product or service life cycle. Leadership is demonstrated by the visible involvement of management in defining and disseminating quality policy. Management creates an environment conducive to employee involvement by :
- Setting clear, measurable objectives
- Allocating the necessary resources
- Valuing improvement initiatives
Strong leadership encourages everyone to adhere to quality principles, stimulating innovation and overall organizational performance.
Process approach and continuous improvement
The ISO 9001 process approach optimizes workflows by identifying the key interactions between the organization’s various activities. This method encourages a cross-functional vision, overcoming traditional functional silos. Process mapping enables critical steps to be clearly visualized, and opportunities for improvement to be identified. For example, a manufacturing company can reduce production lead times by analyzing and optimizing the flow of raw materials. Continuous improvement, on the other hand, relies on the PDCA cycle (Plan, Do, Check, Act) to systematize progress. Organizations implement performance indicators (KPIs) to measure the efficiency of their processes and define realistic improvement targets. This dynamic approach stimulates innovation and strengthens long-term competitiveness.
Evidence-based decision-making
Rigorous data analysis is the cornerstone of effective management. Organizations systematically collect and evaluate relevant information to guide their strategic choices. For example, a manufacturing company might use dashboards to track defect rates (non-conformities) and identify areas for improvement. A customer service department might analyze consumer feedback to adjust its offerings. This fact-based approach makes it possible to :
- reduce decision-making bias
- optimize resource allocation
- anticipate market trends
The use of predictive analysis tools strengthens management’s ability to make informed decisions in the face of complex external challenges. A regular review of key indicators ensures that actions are aligned with the organization’s strategic objectives.
Key requirements of ISO 9001
Organizational context and leadership
ISO 9001:2015 emphasizes the importance of understanding the company’s operating environment. This analysis encompasses internal factors such as corporate culture and staff skills, as well as external elements such as the regulatory framework and competition. The standard also requires the identification of relevant stakeholders and their expectations. This may include suppliers, business partners and regulatory authorities. The role of management is evolving towards strategic steering of the quality system. Management must align quality objectives with the company’s overall strategy, and promote a culture of improvement at all levels of the organization.
Planning and risk management
ISO 9001:2015 places proactive risk management at the heart of the quality system. Organizations must systematically identify potential threats and opportunities for improvement linked to their activities. This involves:
- The use of risk assessment matrices
- Setting up mitigation plans
- Regular monitoring of the effectiveness of measures taken
The standard advocates the integration of risk management into all operational processes. For example, a company can anticipate supply disruptions by diversifying its suppliers. The risk-based approach stimulates innovation and strengthens organizational resilience in the face of market challenges.
Support and resources
Implementing an ISO 9001 quality management system requires adequate resources. Organizations must allocate competent personnel trained in quality principles. Technical infrastructure, such as measuring equipment and IT tools, plays a crucial role in monitoring processes. A dedicated budget is essential to cover the costs of training, documentation and audits. Organizational knowledge management enables us to capitalize on feedback and optimize practices. Effective internal communication helps raise staff awareness of quality objectives. Management involvement ensures that the necessary resources are available for continuous improvement of the system.
Operational activities
Implementing ISO 9001 at operational level involves optimizing the organization’s key processes. Companies define measurable performance criteria for each stage of production or service. For example, a car manufacturer might establish quality controls for each assembly phase. A consulting firm might institute systematic peer reviews of deliverables. Change control is essential. Organizations document and assess the impact of any operational change before it is implemented. Management of external service providers is an integral part of the system. Companies establish rigorous selection criteria and regularly assess their suppliers’ performance. Traceability of products and services guarantees the ability to identify and resolve potential problems quickly.
Performance assessment and improvement
Performance assessment is a cornerstone of the ISO 9001 system. Organizations implement precise indicators to measure process efficiency and customer satisfaction. Regular internal audits identify gaps and opportunities for improvement. Analysis of the data collected feeds into decision-making and guides corrective action. Management periodically examines results in structured reviews, adjusting quality objectives where necessary. Continuous improvement is based on the Deming wheel (PDCA): plan, do, check, act. This systematic approach encourages innovation and strengthens long-term competitiveness. Non-conformities are treated as learning opportunities, stimulating the evolution of practices and the ongoing optimization of the quality system.
The management review: a key moment
The management review represents a fundamental step in the ISO 9001 quality management system, and in particular in the implementation of the principle of continuous improvement. This periodic meeting enables management to assess the overall effectiveness of the system, and to make strategic decisions. During this review, management examines :
- Results of internal and external audits
- Customer feedback and process performance
- Status of corrective and preventive actions
- Changes that may affect the quality system
This in-depth analysis leads to concrete actions to improve the system, allocate the necessary resources and adjust quality objectives. The management review thus promotes alignment between the company’s strategy and its quality system, reinforcing its long-term effectiveness.
ISO 9001 audit and certification: a tool for improvement
Benefits of ISO 9001 certification
What are the benefits of ISO 9001 certification for a start-up?
Benefit no. 1: improved quality and customer satisfaction
ISO 9001 certification acts as a catalyst for operational excellence. It encourages companies to optimize their processes, thereby reducing errors and production delays. The customer-centric approach encourages more fluid communication. Companies set up regular feedback channels, enabling them to anticipate future needs. This proactive approach often results in increased customer loyalty and positive word-of-mouth. Standardized procedures guarantee consistent quality, regardless of the employee involved. This uniformity reassures customers and reinforces their trust in the brand. What’s more, the emphasis placed on ongoing staff training contributes to innovation and improvement of products and services.
Benefit no. 2: process optimization and cost reduction
Implementing ISO 9001 means substantial savings for companies. This is due to several factors:
- Streamline workflows, eliminating redundant tasks
- Reduce errors and rework, minimizing wasted resources
- Better inventory management, optimizing stock levels
For example, a manufacturing company saved €500,000 annually by optimizing its procurement processes. Standardized procedures also boosted productivity by 20%, without increasing headcount. Analysis of the data collected under ISO 9001 enables bottlenecks to be identified quickly and corrective action taken, maximizing the use of resources.
Benefit no. 3: competitive edge in the marketplace
ISO 9001 certification provides companies with a differentiating advantage in a competitive business environment. It enhances credibility with partners and facilitates access to new markets, particularly internationally. Many organizations demand this certification from their suppliers, creating additional business opportunities. The standard also fosters innovation by encouraging analysis of the economic context and anticipation of future needs. Adopting ISO 9001 improves organizational resilience in the face of market challenges. It enables you to better manage risks and adapt quickly to change, conferring a lasting strategic advantage. The international recognition of the standard strengthens your organization’s position in tenders and commercial negotiations, giving it leverage to stand out from the competition.
The ISO 9001 certification process
5 essential steps to certification
- The road to ISO 9001 certification begins with an in-depth self-assessment of the company’s current practices. This analysis compares existing processes with the requirements of the standard.
- Next, the organization draws up an action plan to close the gaps identified. Staff training in quality principles is crucial at this stage.
- Once the quality management system is up and running, an internal audit verifies compliance. The results guide final adjustments.
- The next step is to select an accredited certification body. This body carries out an initial audit in two phases: a document review followed by an on-site assessment.
- Once any non-conformities have been corrected, the organization issues the ISO 9001 certificate, which is valid for three years, subject to annual surveillance audits.
Role of accredited certification bodies
Accredited certification bodies, such as AFNOR Certification, play a key role in the ISO 9001 certification process. Their technical expertise guarantees a rigorous assessment of quality management systems, their compliance with the requirements of the standard, and the overall effectiveness of the quality organization. As an accredited body, AFNOR Certification ensures the impartiality of audits, essential to the credibility of certification. Their accreditation by national bodies such as COFRAC in France attests to their competence. Accredited bodies :
- Carry out in-depth on-site audits
- Issue detailed reports identifying strengths and areas for improvement
- Issue ISO 9001 certificates to compliant companies
- Ongoing monitoring helps maintain the value of certification over the long term.
VIDEO: Why use an accredited certification body?
Duration and validity of the ISO 9001 certificate
The ISO 9001 certificate remains valid for three years from the date of issue. During this period, the certified organization must maintain its quality management system in conformity with the requirements of the standard. Annual follow-up audits are carried out to verify continued compliance. These regular checks ensure that the organization maintains its good practices and pursues continuous improvement. Before the certificate expires, the company must undertake a full renewal audit. This process, similar to the initial certification, provides an in-depth assessment of the entire quality system. Once validated, a new three-year cycle begins, ensuring the continuity of the quality approach within the organization.
Did you know?
Internal audits are a valuable self-assessment tool for organizations. Conducted by trained employees, they offer a critical look at internal processes and stimulate innovation.
External audits provide an independent perspective. Conducted by industry experts, they compare the company’s practices with industry standards and legal requirements.
Thecertification audit represents the most in-depth evaluation. Conducted by an accredited organization, it scrupulously verifies the quality system’s compliance with ISO 9001 requirements. Successful completion of the audit leads to certification, reinforcing the company’s credibility in the marketplace.
ISO 9001 auditor skills and training
ISO 9001 auditors develop a set of key skills to carry out their mission effectively. Mastery of auditing techniques and in-depth knowledge of the standard are essential. Auditors acquire this knowledge through specialized training courses, combining theory and practice. Critical analysis and clear communication skills are essential. Auditors cultivate these qualities through role-playing and case studies. Technical know-how in the sector audited adds value to the audit. Ongoing training keeps auditors up to date with developments in standards and the sector. Auditor certification, issued by recognized bodies, attests to these skills and reinforces the credibility of our professionals in the marketplace.
Quality management and global performance
Do you have a long-standing commitment to an integrated quality or QSE approach? Are you looking for new levers to drive your approach? Would you like to upgrade your management system to incorporate the challenges of sustainability, corporate culture, agility and organizational transformation? You’ve come to the right place! Our international survey of 1,800 quality decision-makers from all over the world in 2023 has highlighted the future evolution of the quality function. Among the new issues to be integrated: CSR, digital, quality perceptions concerning ethics and organizational values, all of which organizations need to consider to ensure their long-term development.
Integration and complementarity of quality and CSR approaches (or QSE and CSR): towards a sustainable and responsible approach to quality
Quality and CSR approaches are not contradictory, and one is not a substitute for the other.
On the other hand, their integration can ultimately enable a 360° measurement of an organization’s performance, based on a management system.
For this purpose, it is useful to refer to recommendations such as ” Le guide sur l’intégration de la responsabilité sociétale basée sur l’ISO 26000 dans un système de management” XP X30-036.
How can you leverage your quality management system to meet the regulatory challenges of sustainable development?
The main aim of the Corporate Sustainability Reporting Directive (CSRD) is to harmonize corporate sustainability reporting and improve the availability and quality of published ESG (environmental, social and governance) data. Consequently, the support of a Quality Management System coupled with a CSR approach already enables ESG data to be taken into account.
Quality culture: how to encourage and strengthen staff involvement
Employee buy-in is crucial to the success of any quality initiative. A strong quality culture fosters customer satisfaction, improves your processes and gives meaning to the tasks entrusted to you. Although today’s companies have organizations in place, constantly improving technological processes and ambitious strategies, many of them are finding that their quality fundamentals have been lost or have deteriorated. In a context that demands organizations to be as agile as possible (external growth, integration of new employees, customer requirements, new technologies, etc.), the fit between strategy, values and Quality practices is not always as fluid.
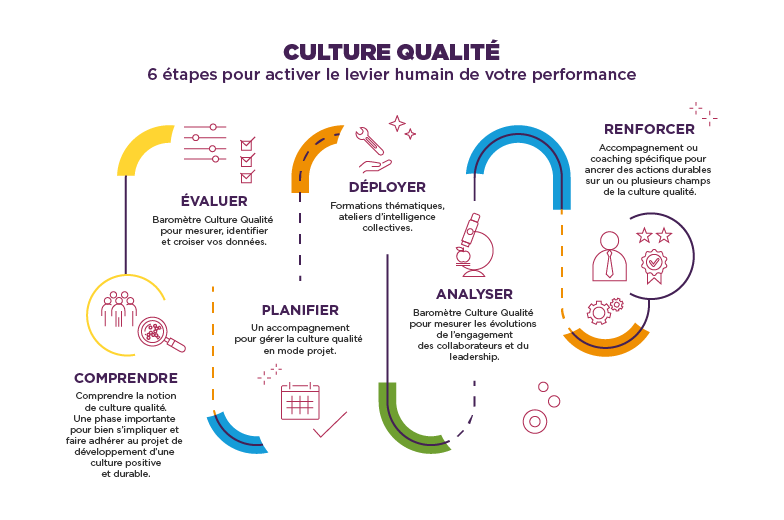
Step 1: Understanding
Aimed at management and executive committees, facilitation workshops help to understand the concept and challenges of a strong quality culture, to establish an initial diagnosis, and to establish a shared vision and clear objectives for reinforcing the quality culture.
We also recommend reading the ISO 10010 standard, which offers recommendations for assessing, developing and improving quality culture within the organization.
Step 2: Evaluate
Beyond management teams, it’s essential to measure quality culture at all levels of your organization. To help you do this, we have developed the Quality Culture Barometer. A veritable compendium of the Afnor Group’s quality expertise, it enables you to objectively assess your employees’ perception of your company’s quality culture.
The Quality Culture Barometer breaks down into several levels, allowing you to display your quality culture mapping along 9 axes (based on a 5-minute anonymous survey of your employees). You receive a report analyzing your situation and your Net Promoter Quality Score. Options allow you to deepen your analysis by cross-referencing data by theme, by site, and by comparing you with other organizations, providing you with a rich benchmark. You can also supplement quantitative data with qualitative interviews with several employees, to give concrete expression to the results of online employee feedback.
Step 3: Planning
This stage completes the analysis stage: once the gaps between the perceived quality culture and the quality culture promoted have been identified, Afnor’s support helps you to select the areas to be strengthened, prioritize your subjects, and identify the tools and formats needed to bring your project to a successful conclusion.
Step 4: Deploy
At this stage, you need to get your staff on board and support the spread of your quality culture. To achieve this, participative workshops are used to involve teams in the development of new working methods. This collaborative approach reinforces a sense of ownership and reduces resistance to change. Built around the themes identified by the barometer, it will be all the more relevant. Training also plays a key role in adapting to new practices. Regular sessions for managers or a network of quality culture ambassadors will help teams understand their role in continuous improvement. First-level awareness-raising can also be offered to operational teams to get them started on the road to quality.
Step 5: Analyze
At this stage, it may be a good idea to start listening to employees again, using the quality culture barometer to measure changes and employee commitment, and then to set new ambitions or devise new approaches to further strengthen the quality culture.
Step 6: Reinforce
Finally, we can provide support over time to prevent the process from running out of steam. Depending on your needs, we can offer targeted collective intelligence workshops, coaching sessions for your managers, or customized training courses. We are at your side to build the best response to your needs.
EFQM
Do you have several performance initiatives in place (quality, environment, CSR reporting, certifications required by your customers…) and would like to manage them consistently? Give new impetus to your approach or build an action plan to implement and support change? Assess and gain recognition for the excellence of your practices?
EFQM can meet your needs. Nearly 50,000 organizations worldwide rely on this model, which is now available as a free download.